A great reality in the world of by-products of animal origin.
A family story
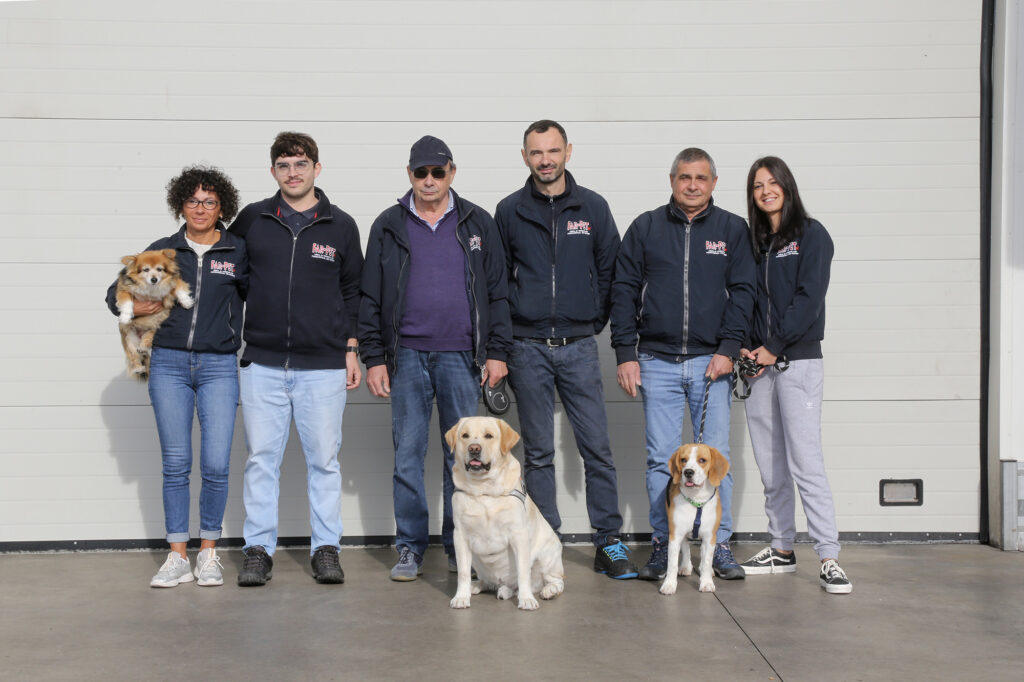
Far-Pet was born in 2008 when the Beruffi brothers, after forty years of experience in the sector of marketing animal by-products, undertook to build the plant in Castel Goffredo (MN).
Over the years Far-Pet has invested in the expansion of its factory and in supporting technology by collaborating with slaughterhouses and natural casing processing companies.
The company, recognition number ABP930INTP3/ ABP930TRADE3 has developed its own production processes under the careful control of the health authorities, in full compliance with the reference legislation EC Reg. 1069/09 – EU Reg. 142/11 and subsequent amendments. and is registered pursuant to art. 9 paragraph 2 of Reg (EC) 183/2005 as Feed Sector Operator in the list of the Lombardy Region.
FAR-PET then developed the wholesale trade of food for human use “without deposit” of frozen products of animal origin intended for transformation and subsequent use in the food industry, duly authorized by SUAP reg.852/04 notification. : N° 02224760203-16012017-1837.
To date, FAR-PET is a reliable resource and point of reference for numerous categories of customers, providing various services ranging from fresh to frozen products.
The business is located in the center of Northern Italy, between the provinces of Brescia, Parma, Cremona, Modena and Mantua in the heart of pig slaughtering. The strategic position allows the daily collection of the raw material at a national level, thus consolidating the national and international collection and sales network.
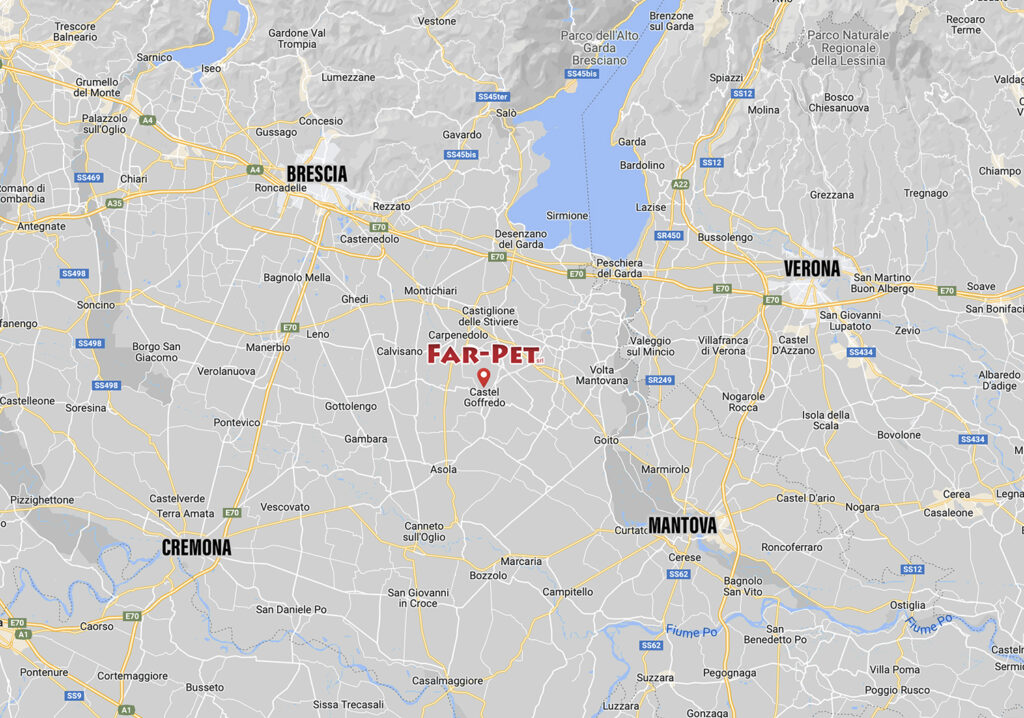
Far-Pet aims to meet the highest quality standards in compliance with the legislative criteria of the animal by-products sector, to protect the wholesomeness of the product through various phases:
- Careful selection of suppliers
- Careful quality control
- Refrigeration and freezing
- Storage and deposit at controlled temperatures
- Safe monitoring and maintenance of the cold chain
ESTABLISHMENT
From 2008 to today, Far-Pet has doubled the square footage of the plant, expanding both the production space and the space dedicated to the storage and freezing of goods. The temperature-controlled storage cells are equipped with probes connected to a recording software for detecting temperatures. The company that supplies the freezing systems monitors the proper functioning and maintenance of temperatures 24 hours a day through an automatic monitoring and recording system.
The company consists of two adjacent buildings of approximately a total of 2,365 square meters:
Warehouse A, which occupies a total area of 900 m2, of which:
- 500 mq of storage cell;
- 150 mq of freezing cell;
- 150 mq of pallet preparation room;
- 100 mq of premises used as offices / services and changing rooms.
Warehouse B, which occupies a total area of 1465 m2, of which:
- 215 mq of frozen goods storage cell;
- 230 mq of cooling cell;
- 180 mq of pallet preparation room;
- 100 mq of premises used as offices / services and changing rooms.
- 350 mq of frozen goods storage cell.
- 390 mq of a room that houses an automatic vault / crate washing machine, metal detector and pallet preparation area.
GREEN ENERGY
Far-Pet, always attentive to innovation in its structures, has invested in renewable sources by installing a 499.56 kWp photovoltaic system, demonstrating the company’s commitment to contributing to the improvement of everyone’s quality of life while respecting the environment, safety, health, and product quality.
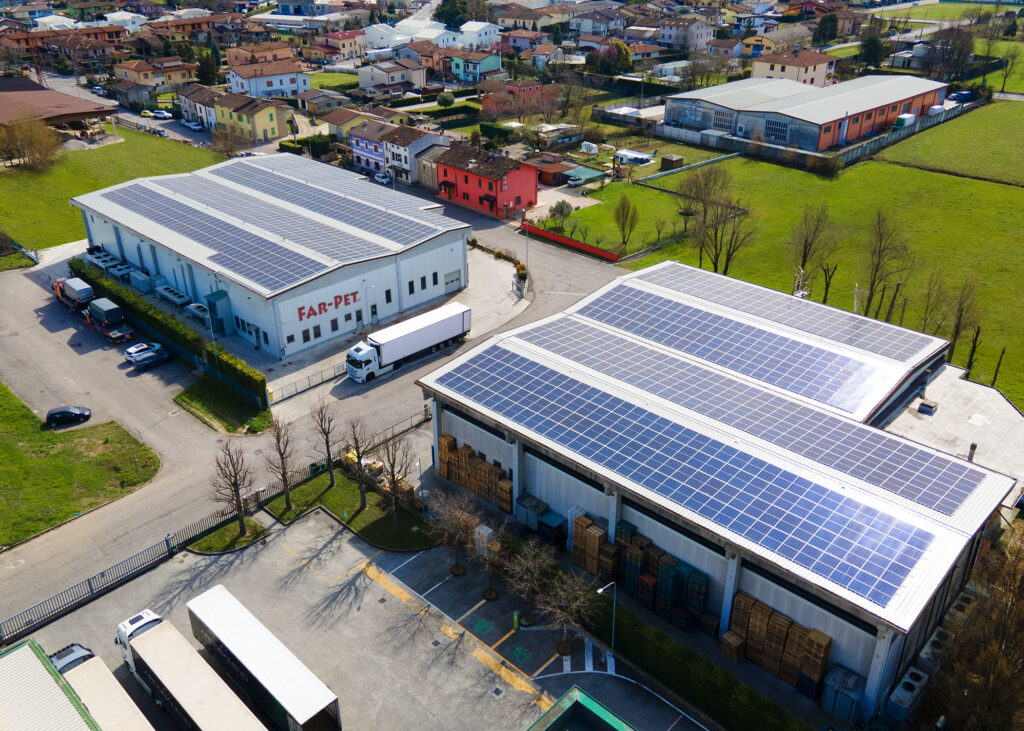
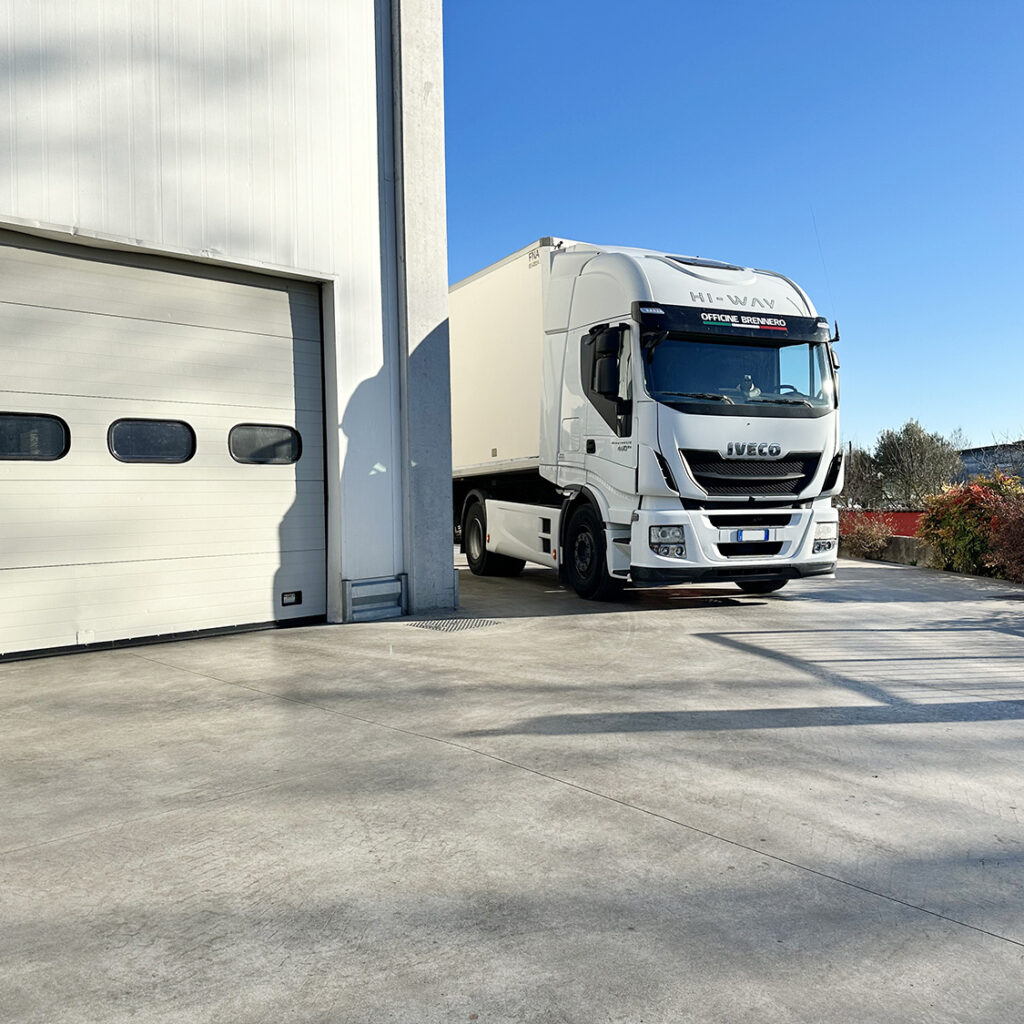
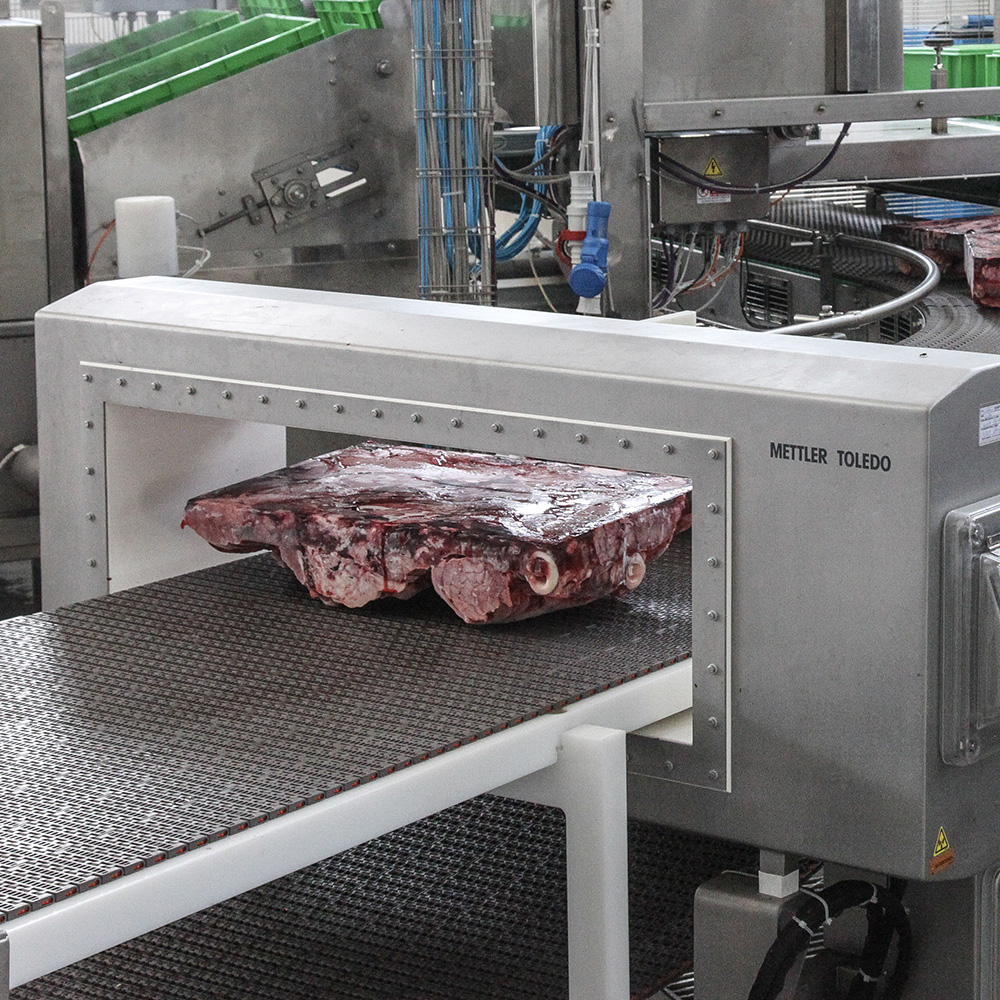
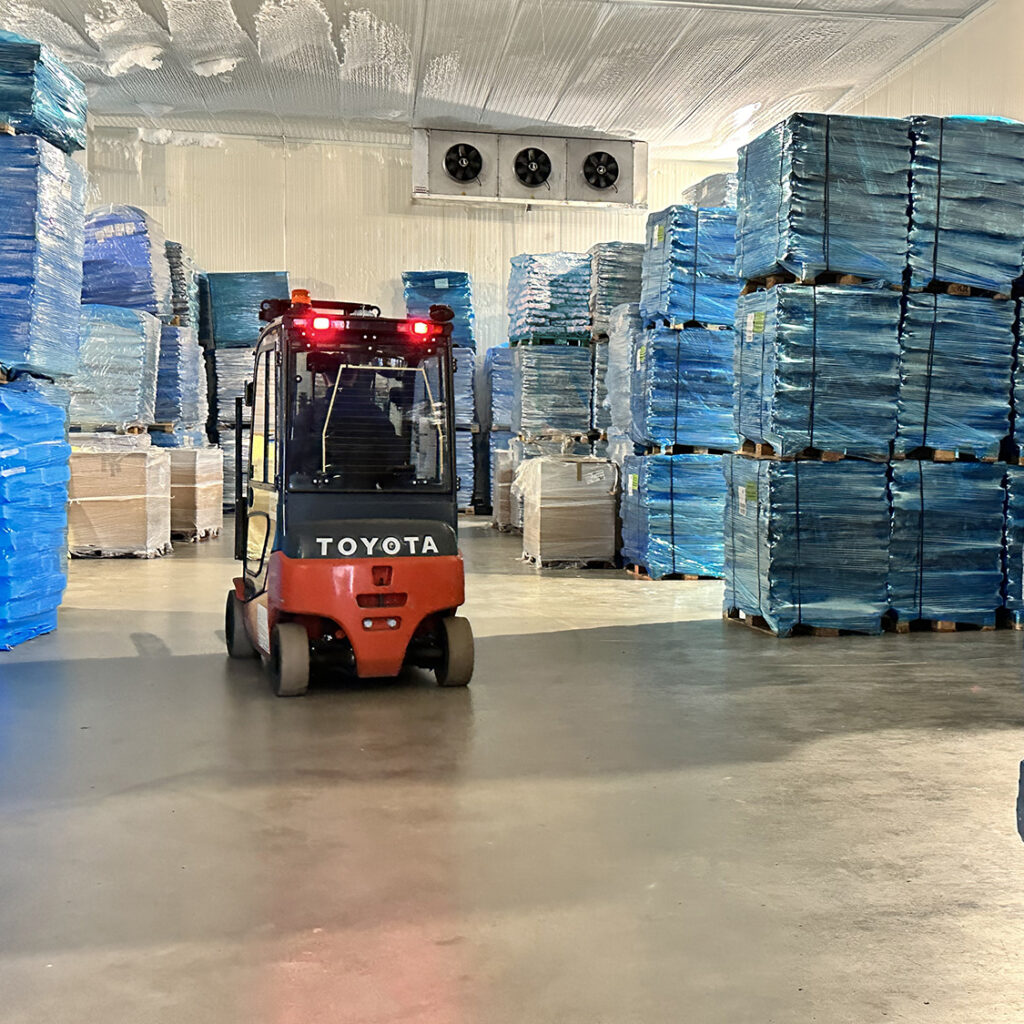
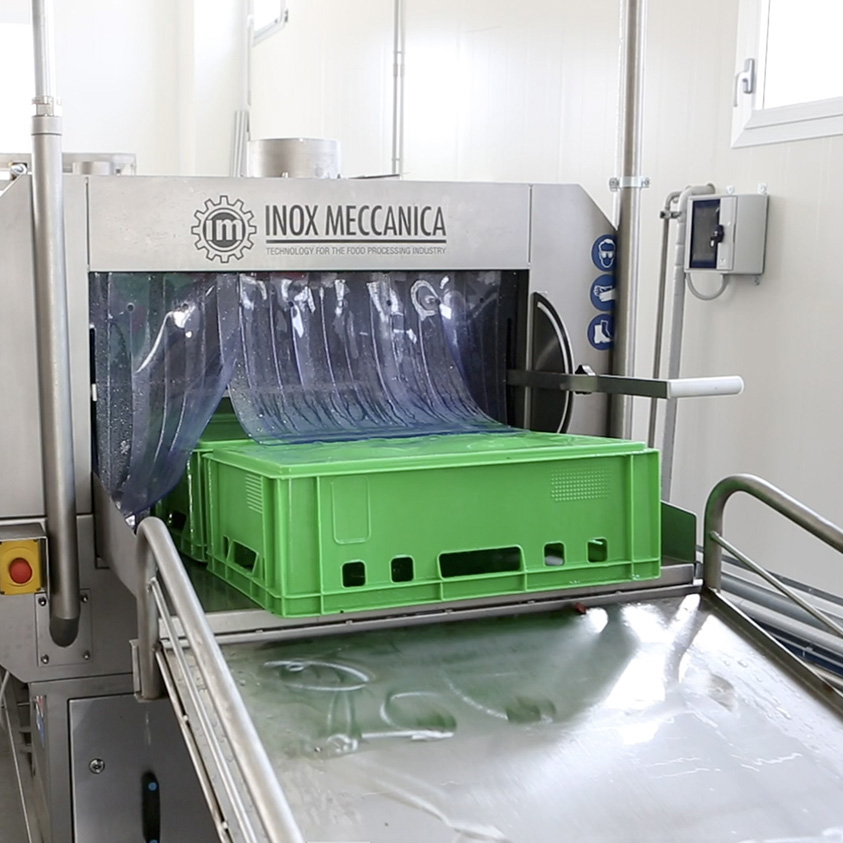
CHECKING OF FROZEN STORAGE AREAS
COMPUTERIZED WAREHOUSE MANAGEMENT SYSTEM AND REMOTE ASSISTANCE
FAR-PET is equipped with temperature-controlled storage areas.
This system includes:
- Graphs that allow the trend of the stored variables to be consulted on screen and on paper in the form of graphs or tables.
- Alarms, with recording of the date and time of the event and of the end of the event.
- History of all operations performed by the “remote control center” with connection date and time recording.
- Consultation and printing of events and graphs with archiving of at least 2 years.
- Haccp in compliance with the EEC directive 93/43, which determines the obligation for the producer of self-certification regarding the hygiene and quality of food.
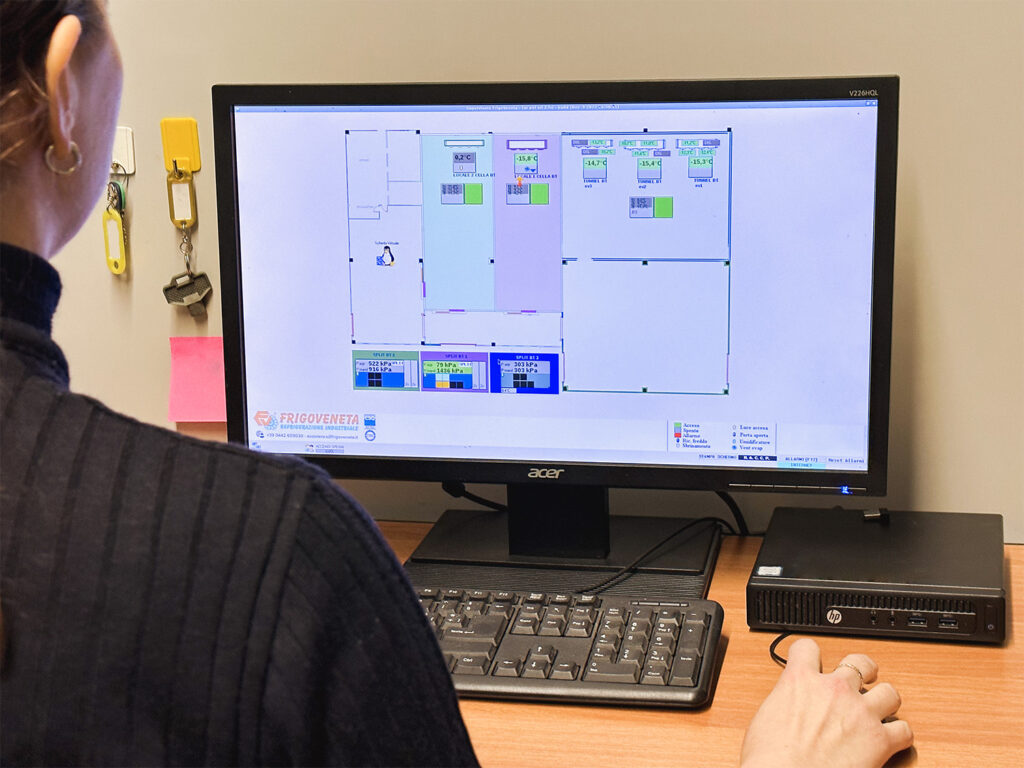
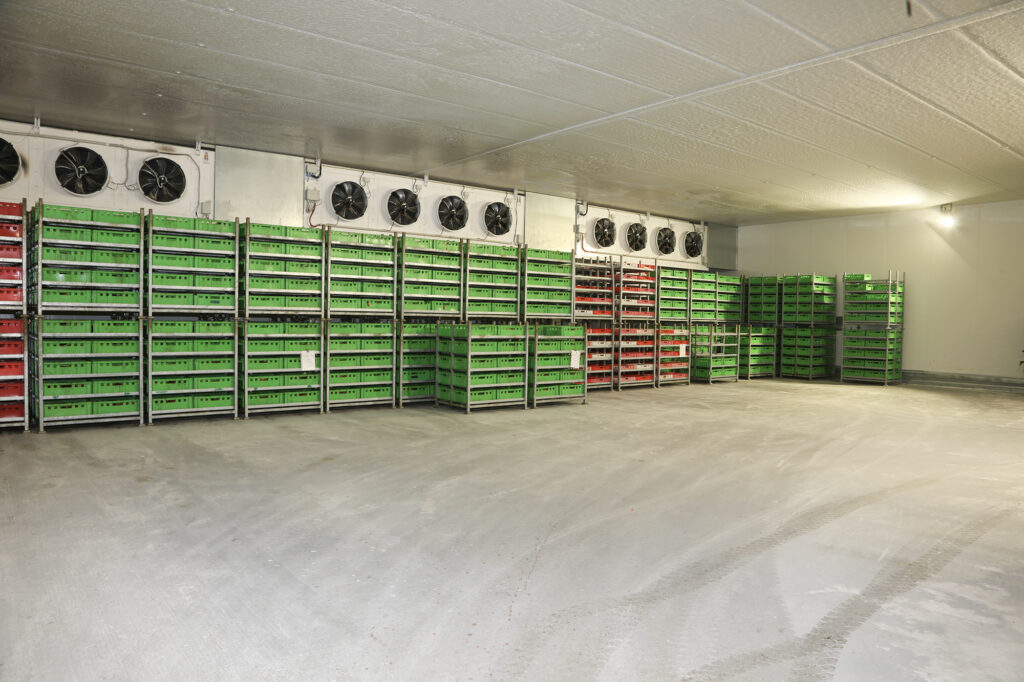
FREEZING TUNNEL
Abatement tunnel at an average temperature of -30° which allows the fresh goods arriving in the afternoon from the slaughterhouses to be quickly brought (the following morning) to the expected standard temperature (about -18°) to be placed in the preparation chain for delivery to the customer or for warehause freezing area.
FROZEN OR REFRIGERATED WAREHOUSE
Freezing area with an average temperature of -18° (for frozen products) and -4° (for fresh products) used for the storage of goods awaiting delivery to the customer.
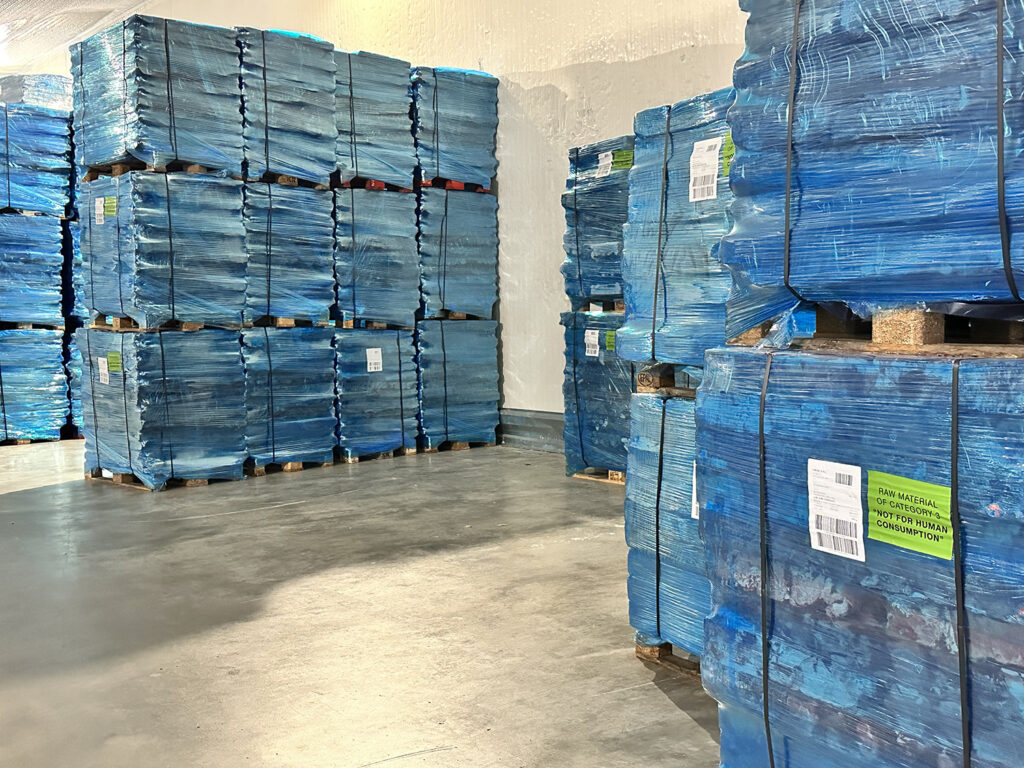
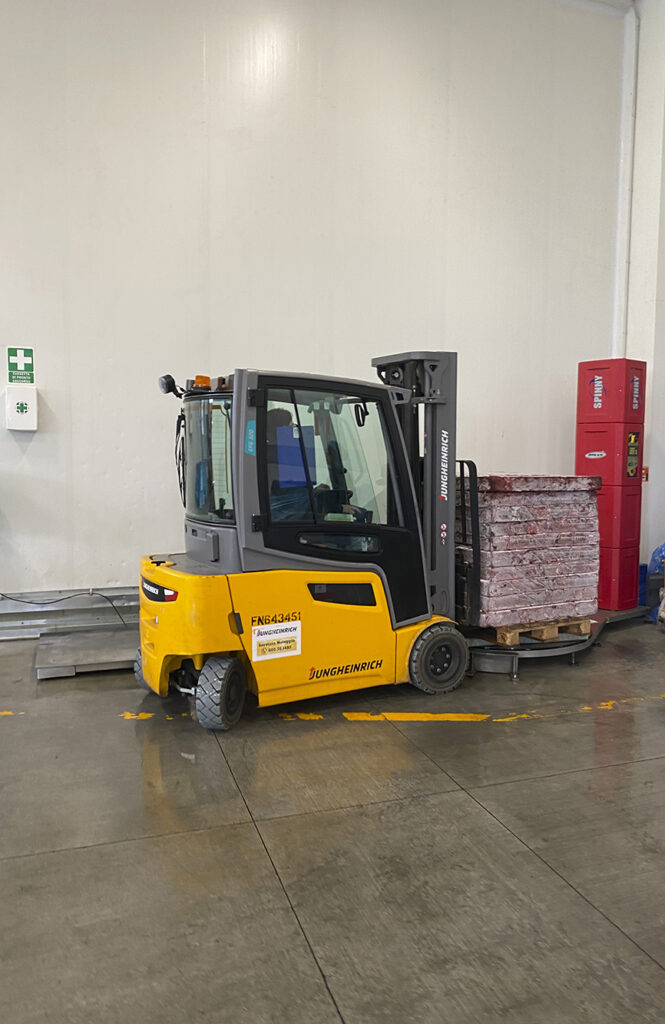
ORDER PREPARATION AREA AND PALLET SETUP
Inside its factory, FAR-PET has special areas (720 square meters in total) adjacent to the freezing area which allow the preparation and palletisation of the fresh or frozen product for the fulfillment of customer orders or the storage freezing area awaiting the fulfillment of the same orders.
These areas are accessible only in compliance with the provisions of the hygienic-sanitary self-control procedures and with the regulations on safety in the workplace.
INNOVATIVE INSTALLATIONS
Box-turning machine expressly designed for Far-Pet which allows, at the end of the freezing of the raw material, a quick, safe and healthy extraction of the product from the plastic boxes that contain it. Once the product has been extracted from the crates via the plant’s conveyor belt, it is brought under the metal detector and subsequently palletized, while the crates immediately pass into the crate washer, to be washed and sanitized and available to be sent back to the slaughterhouse.
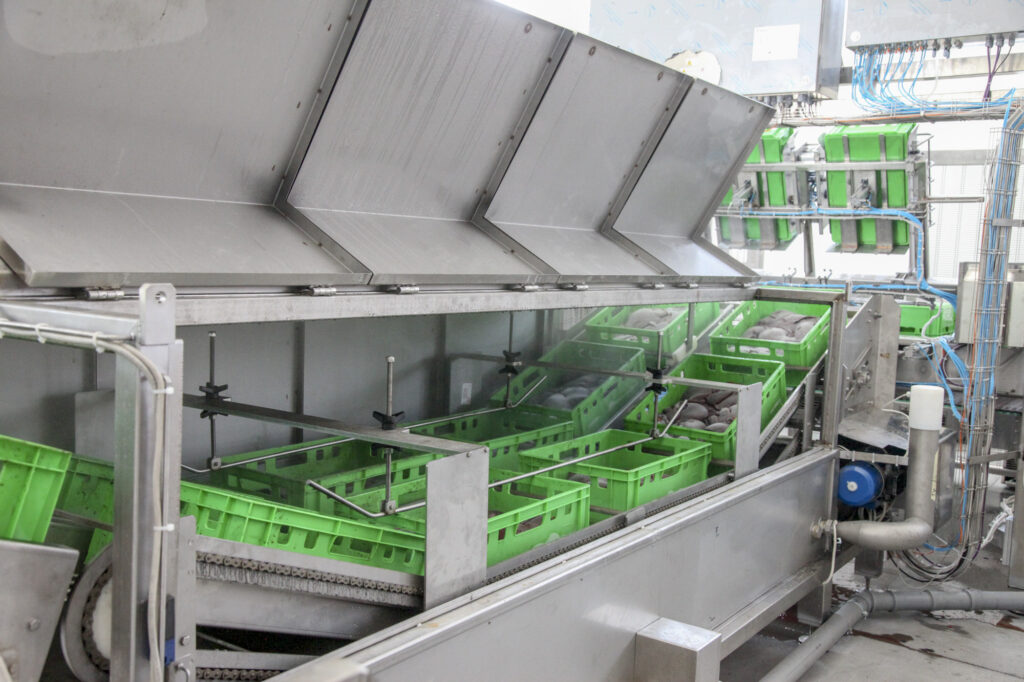
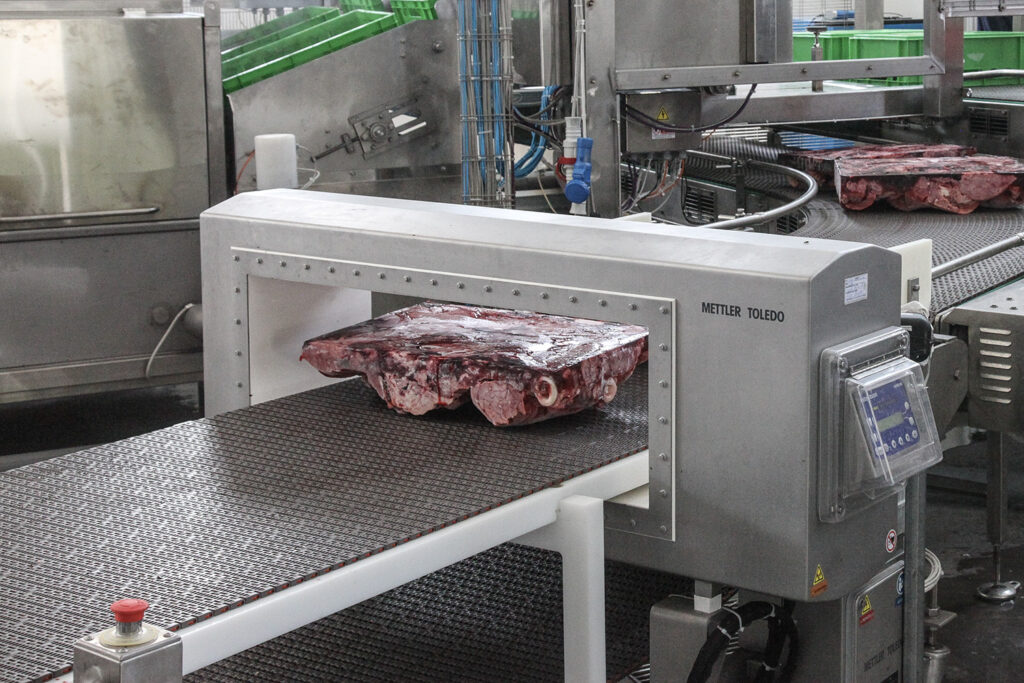
METAL DETECTOR
Far-Pet has included in its line the control for the presence of foreign bodies, through a metal detector regularly calibrated by its manufacturer and calibrated internally every day before being put into operation.